Canada’s Venture Composite Index (a basket of economically sensitive micro-cap companies, 44% weighted in materials, 30% information technology, 15.74% in energy, 3.5% health care, 2.48% financials, 1.85% industrials, .58% communication services, and .32% consumer discretionary) appears to concur with former BoC head Stephen Poloz’s recessionary assessment.
When the real economy expands, rising demand for commodities and commodity-centric companies should reflect that. We saw this from 2009 through 2011 and briefly from 2020 into 2021.
Today (as shown below since 2000, courtesy of my partner Cory Venable), the Venture Composite Index is priced 41% below its 2021 top, 81% below its May 2007 cycle top, and 20% below its November 2008 “great recession” bottom.

Meanwhile, the large-cap TSX composite stock index (33% in financial shares) rebounded sharply in the past year to reach 17% above where it topped 33 months ago in March 2022 (below since 1980).
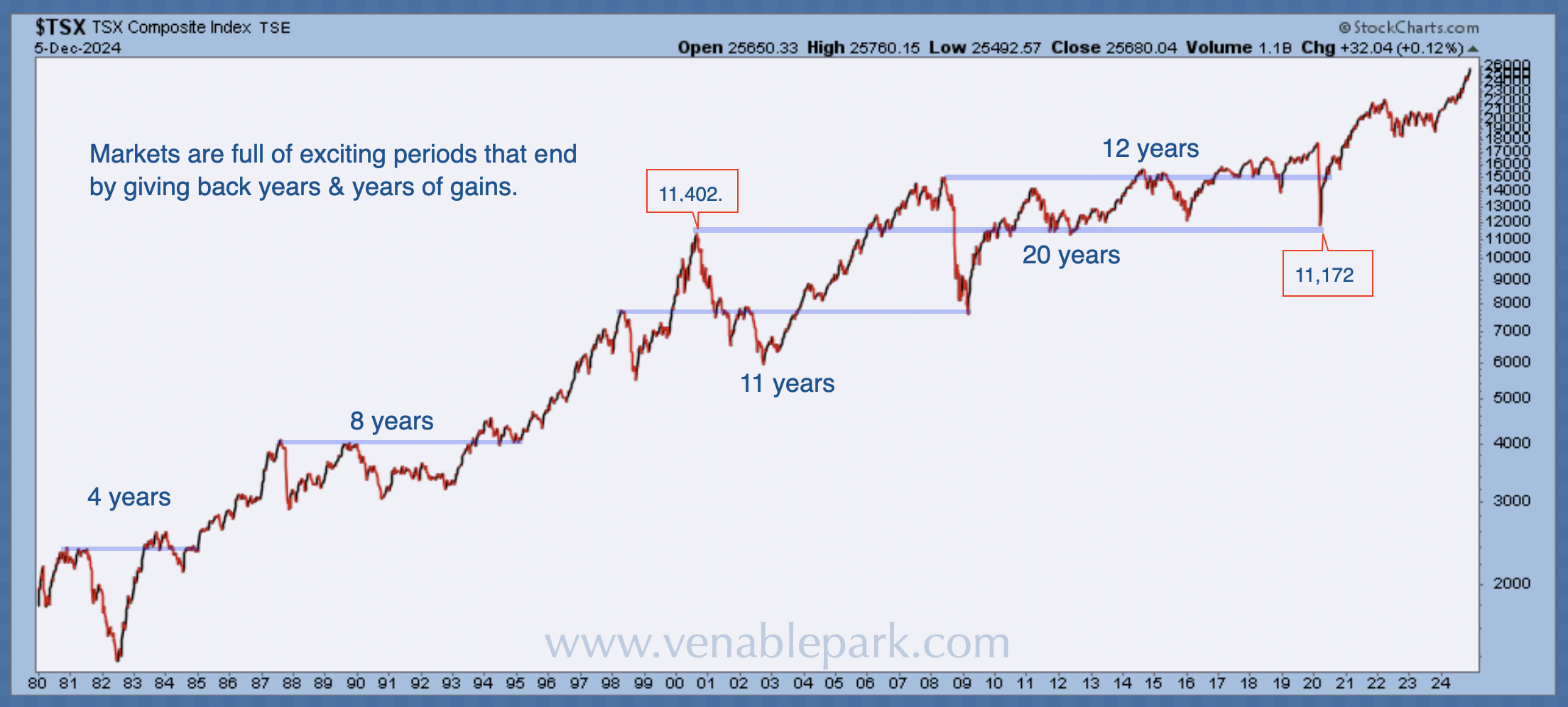
It’s important to note that there has never been a recession during which the Canadian stock market did not give back years of prior appreciation. Ladders take you up before snakes take you down. We see this above. In 1980-1982, the TSX dropped -45%, 1990-1993 (-24%), 2000-2003 (-50%, even though Canada technically avoided joining the US in a recession that cycle), 2008-2009 (-50%), and 2020 (-37%).
Apart from the highly irregular COVID drop and rapid 11-month bounce back, the shortest recovery time was 4 years to 1984 to recoup the 1980-82 losses. It took 8 years to 1995 to recover from the 1987 market drop, even though no recession unfolded.
In the 2008 bear market, the TSX dropped back to the price level it had first reached 11 years earlier, in 1998. It took 6 years for the market to recoup its 2008 high by 2014, and it remained range-bound until December 2018, for a decade of flat pricing.
Even that proved fleeting; the TSX gave back 20 years of gains as it tumbled back to the 2000 cycle high in March 2020 (see above). Amid unprecedented monetary and fiscal stimulus following 2008, it still took 12 years for the price index of Canada’s most valued companies to hold above the 2008 cycle peak by May 2020.
The 14% sell-off from March 2022 to last October returned the TSX to the same level as April 2021. At that point, it had managed a 24% gain over more than 15 years and underperformed T-bills with much greater risk and volatility.
The masses have once more been convinced that stocks are the only place to put our savings, but facts do not support that view. People are not pensions. Timing and our finite lifelines are everything. Since 1901, the stock market has spent 76% of the time declining in value or recovering from losses and just 24% of the time making new highs (Ned Davis Research). Fear of losing money should trump fear of missing out on fleeting gains.
Starting valuations are definitive of returns in the longer run, and the higher they are, the harder prices fall. Today, equity risk-reward prospects have rarely been less attractive. This much is true. But history and human behaviour assure us that this shall pass and good things come to those who can carefully manage their emotions and capital over time.